Avoid grain elevator hazards
INNOVATIVE ELECTRICAL MONITORING SYSTEM
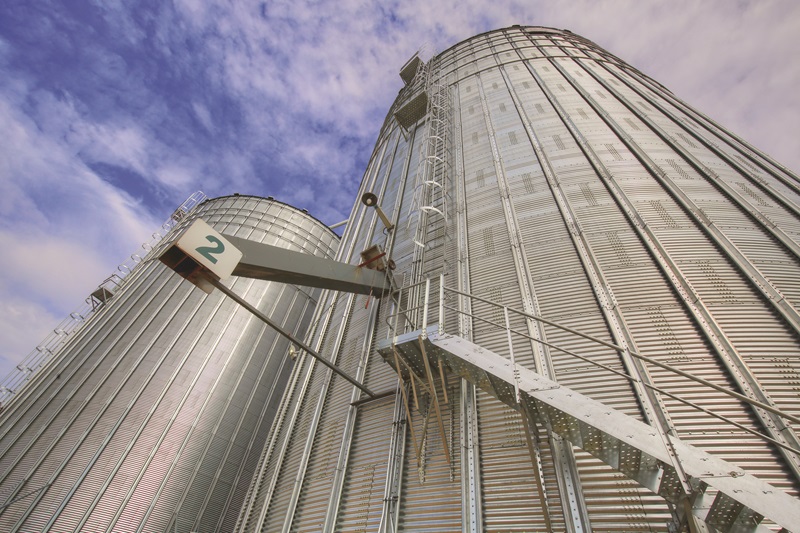
KEEPING CRITICAL EQUIPMENT LIKE GRAIN DRYERS AND FANS operating during peak harvest season is essential to maintaining optimal grain quality and yield. So, how can you prevent breakdowns, or worse, a fire that could lead to considerable downtime, workplace safety issues or lost revenue?
A new electrical monitoring system is now available to detect potential faults, overheating, or irregular equipment performance early to prevent equipment failures and fire hazards. The PrevTech Solution (prevtech.ca) protects grain operations with real-time electrical monitoring and proactive alerts that can be sent straight to a smartphone, along with expert technical support to troubleshoot identified hazards before they cause damage to equipment or the overall operation.
“Grain dryers are an essential piece of equipment for farmers and facility operators, but while they are necessary to help generate quality products and profits, they also pose serious electrical malfunction and fire risks,” says Pierre-André Meunier, president and founder of PrevTech Innovations Inc., a Quebec-based company that specializes in monitoring and preventing electrical fire and business interruptions.
Already proven in livestock barns throughout North America, the PrevTech Solution ensures optimal performance and early detection of electrical issues impacting safety and efficiency and is now available for grain elevators and mills. Meunier explains that “our system not only detects electrical issues but also helps prevent potential hazards before they cause damage, focusing on farm-specific needs.” And in the case of grain dryers and elevators, keeping equipment running smoothly, safely and at peak performance ensures worker safety and grain quality and peace of mind for growers and operators working against variable fall weather to harvest, dry, and store crops.
EFFECTIVE AND EFFICIENT OPERATIONS
PrevTech’s solution can integrate seamlessly into a farm’s risk management plan by proactively detecting electrical issues that could lead to fires, equipment failures, or costly downtime, especially at harvest. This system can be easily installed by a licensed electrician and allows growers to manage their assets and reduce potential risks to their operations.
Meunier points out that something as simple as losing ventilation to a bin can lead to moisture buildup and mould, which can easily jeopardize the quality and value of the grain.
“We understand that during the harvest season, loading and unloading operations are crucial aspects to running at optimal performance,” says Meunier, who shares a recent customer experience, saying, “we were recently able to help a grain operator client quickly by identifying a faulty component. This allowed him to service and replace the component between loads without losing any operating time.”
Not only can the PrevTech Solution help identify electrical or equipment faults in real- time that may need to be addressed right away, but using the system, growers and operators can also detect problems before they occur, like a motor that is increasingly running hot or a breaker that regularly trips.
In such cases, electrical maintenance can be scheduled and performed, preventing unwanted downtime during peak periods, and a call to an electrician during off hours. “There’s nothing more important than keeping your grain dryer and bins running smoothly and safely when you need them most,” notes Meunier.
PROACTIVE PREVENTION
While a robust electrical monitoring system like PrevTech is the ideal solution to minimizing the risk of electrical issues and equipment failure, Meunier reminds growers and grain facility operators that maintenance is still the first step to keeping grain facilities and equipment running safely at peak performance.
Here are Meunier’s top maintenance and fire prevention tips for grain dryers and fans:
- Regularly inspect all electrical systems and connections, especially in high-demand areas like grain dryers and fans.
- Keep electrical panels and outlets clean and free from dust accumulation.
- Install surge protection to safeguard equipment during power fluctuations.
- Monitor equipment for unusual sounds or performance issues that could indicate an electrical fault.
- Clean your grain dryer regularly to prevent the accumulation of combustible materials.
According to Meunier, the most common causes of fires and operational interruptions in grain elevators and mills are dust and debris buildup, wear and tear on equipment, heat (enclosures and circuit breakers can operate at higher temperatures that can cause arching and overheating), and the general environment of a grain facility that often includes highly motorized environments with complex and mechanically demanding electrical loads.
Meunier says he’s proud to provide an innovative solution to help enhance the safety of Ontario grain operations. “Our grain customers report increased peace of mind, noting fewer unplanned downtimes and reduced risks of equipment failures. Farmers appreciate our preventative approach that helps them manage their operations more efficiently and safely,” he says. •