New technology for grain farmers
A YEAR OF INNOVATION
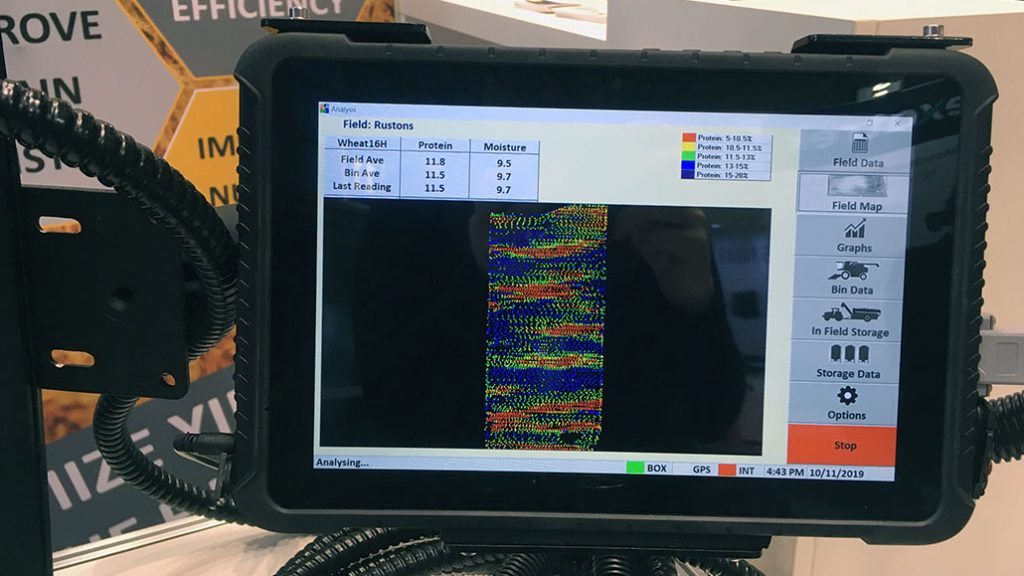
THE RATE OF technological advancement in agriculture in recent years has been nothing short of astounding. Around the world, engineers and equipment manufacturers are designing innovative machinery, advanced robotics, and practical gadgets to improve farm finances and overall efficiency. These advancements promise to do everything from tackling labour issues to reducing energy costs to combating compaction. Here are some of the latest innovations from the past year.
REAL-TIME GRAIN QUALITY ANALYSIS
The CropScan 3300H is an on-combine grain analyser developed by Next Instruments in Australia. Using near infrared technology and a remote sampling head, CropScan analyses protein, oil, starch, fibre, and moisture levels as grain is harvested, and provides a real-time field map as it harvests.
Next Instruments marketing manager Victoria Clancy says farmers use CropScan to segregate grain after harvest or to blend their grain to meet a higher grade. Others use the data to create protein maps, which they overlay with yield maps from the combine to further enhance variable rate strategies.
In 2016, independent crop advisor Steve Larocque bought a CropScan 3400H unit in order to better understand nitrogen mineralization rates and how protein levels vary across the 30,000 acres he manages.
Since Larocque bags most of his grain, using CropScan for segregation is not possible, but he says it is doable for those who are. He is not sure if the math adds up.
Where he thinks the tool has real value, though, is in honing fertilization rates.
In the coming years, he plans to compare environmental conditions with grain data to see which biological, chemical, or structural parameters generate higher protein. He also wants to know if there are any correlations between pH, electric conductivity, or any nutrients and protein.
“It’s a tool to help fine tune your zones, your yield potential inside of each zone, and your proteins, which is ultimately a reflection of your mineralization rates,” says Larocque.
MINIMIZING GRAIN LOSS
Saskatchewan grain farmer Trevor Scherman, co-founder of ScherGain Solution System, says he is embarrassed to admit how much harvested grain he used to lose off the back of the combine, but says it was easily thousands of dollars on his 6,500-acre farm.
In order to calculate the losses, Scherman designed a simple drop pan that magnetically and remotely mounts to the bottom of the combine. Once settings are locked in and the combine has run for a bit, farmers simply drop the pan and transfer the lost grain to a gauge. Scherman has done the math, converting mass to volume.
It is basically a speedometer without numbers, he says.
Scherman recommends growers calibrate the combine anytime a major change is made, not just for crop type, but also variety. Weather events and crop quality can also impact how crop flows through the combine.
Each kit costs just $1,800 and comes with the ScherGain Drop Pan, two remotes, a battery, a grain gauge, and a loss chart. ScherGain works for all crops, including corn, soybeans, and wheat.
CAB COMFORT
The inside of a tractor cab can be a noisy environment. A loud working environment can lead to error and undue stress. To address this issue, German startup-company Recalm has developed a noise-cancelling headrest that focuses on frequencies between 50–500 Hz.
The principle is the same as what is used in noise-cancelling headphones, says Marc von Elling, one of the product’s designers. Microphones record the noise and a processing unit in the back calculates the anti-noise with opposite polarity to the noise source. A signal is then sent out through the speakers to cancel out the noise around the user’s head in the machine.
Recalm is sold as an after-sales item and is easy to integrate into the cabin. It requires a mounted headrest and a power supply (12 or 24 volts). Because most tractors do not have headrests, Von Elling says they are working with equipment manufacturers to integrate them at the design stage.
Recalm cannot cancel all noises, but the aim is not to cancel everything. Drivers will still want to hear the engine, especially to gauge workload, says Von Elling.
The second component that could improve cab comfort in the future is an adaptive armrest. Designed by engineers at the University of Hohenheim and German start-up company Elobau, the adaptive armrest makes control of implements that use PTO and hydraulics easier.
Each adaptive control element is assigned a function symbol that corresponds to the controlled function of the implement, making identification clear for users, explained Timo Schempp, research associate at the University of Hohenheim.
The actuation direction of each operating element can be adapted to an up/down or a forward/backward function to meet expectation requirements and motion compatibility, he says.
When they are not in use, controls are hidden to further improve clarity and ease of operation. The armrest also includes a joystick that can be used in several ways or completely hidden.
Once activated, the operating mode selector switch enables only the required functions; controls for hydraulic functions can only be accessed if they are assigned a function.
Another challenge the adaptive armrest addresses is switching from road mode to work mode or vice versa. Doing so requires a number of functions, including locking and unlocking hydraulics and/or the linkage. It can also manage tasks such as activating and deactivating traction management, and the hydraulic folding of attachments such as spray booms.
The mode selector switch enables these functions to be accessed and controlled as a group. Only relevant functions and controls can be activated.
PEST AND DISEASE MANAGEMENT
German manufacturer Geringhoff received high praise at Agritechnica 2019 for Horizon Star III Razor, a corn head designed to break stalks and stubble down during the cutting pass. Their aim was to destroy stubble that provides shelter for overwintering corn borer and fusarium. It is a tool that has become especially important in parts of Europe where GM technology is banned and pesticide use is limited.
The corn head uses three-roller Rota Disc technology to thoroughly shred the stover by pulling the stalks through counter-rotating disc rotors with 15 cutting discs that engage in the two slotted snapping rolls, explained Dirk Straeter, director of marketing at Geringhoff.
The stalk chopper distributes the shredded stalk, and as the chopper spins to distribute the material, the new rotating tool cuts the stubble. The cutting edges hit the stubble at an angle, ripping it down to the root when the horizontal blade makes the cut at ground level.
Horizon Star III Razor’s design is what makes it possible for the header to cut so close to the ground, explained Straeter. The frame is split in the middle and consists of two sections for independent contouring. Each section has a height control sensor, and a third sensor in the centre of the machine controls the height of the feeder house.
While stubble can be managed post-harvest using a flail mower, one of the big benefits of the Horizon Star III Razor is that it completes two tasks in one, which saves time and costs. But most importantly, it reduces shelter options for the corn borer and leads to the rapid breakdown of straw, which reduces fusarium pressure in the following crop.
All four of the above innovations were seen firsthand at Agritechnica, the world’s largest trade fair for agricultural machinery. The event is held every two years in Hanover, Germany and draws more than 450,000 people.
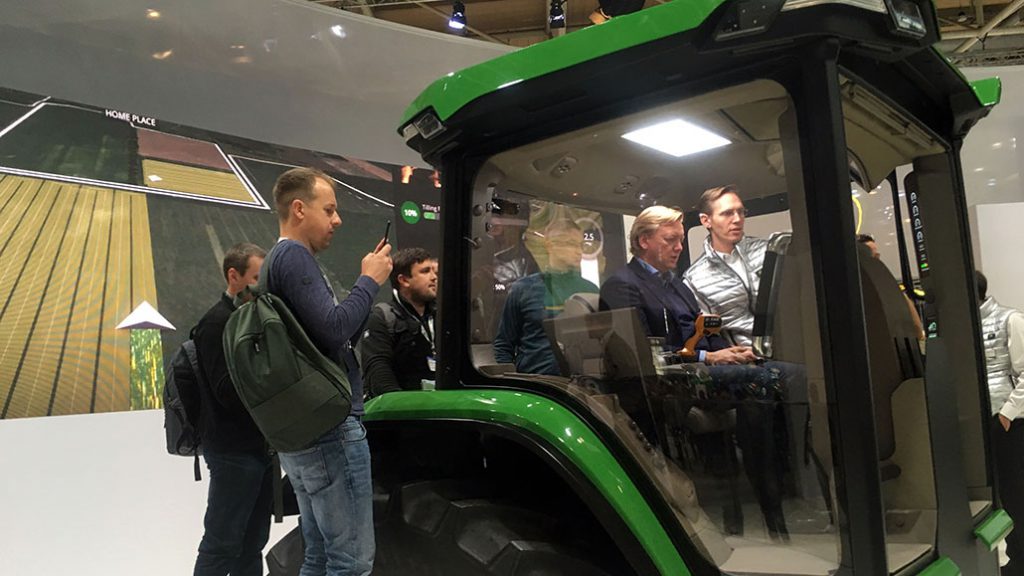
FUTURE VISION
While it was nearly a year ago when John Deere wowed the crowd at Agritechnica, its vision remains futuristic. The manufacturer showcased nine product developments featuring electrification, autonomy, and artificial intelligence, conceptualizing their vision of a more productive and more sustainable future.
First, John Deere gave the tractor cab a complete overhaul. The Command Cab of the future combines joystick control and touchscreen display, and connects all machine components in one place, making for an entirely unique operating concept. The Command Cab is linked to real-time weather data, job management software, and preset tasks, effectively making the cab the command centre for the entire operation.
Above the cab, there was a large spraying drone, called the VoloDrone. Jointly designed with Volocopter, it is 9.2 m in diameter and can be operated both automatically and remotely. It is equipped with two liquid tanks, a pump, and a spray bar.
Eighteen rotors power the drone sprayer, and it runs on a fully electric drive complete with replaceable lithium-ion batteries. Each battery offers 30 minutes of flight time; the drone can spray approximately 15 acres each hour.
The Future Technology Zone also showcased a zero-emission compact utility tractor with high PTO power. It is well suited for use in areas that require low noise levels and emission-free operation.
Autonomy was another big theme in the Future Technology Zone where John Deere featured an autonomous electric tractor, a semi-autonomous tractor, an autonomous sprayer, and autonomous drone sprayer.
The autonomous electric tractor concept is a very compact unit. The tractor has a total output of 500kW. It can be outfitted with wheels or tracks. The electric drive eliminates operating emissions and noise, and the design reduces soil compaction.
John Deere’s Future Technology Zone also featured a semi-autonomous tractor that’s equipped with an integrated crop sprayer. The machine is designed to work in row crops using a built-in camera. The sprayer tank on the semi-autonomous unit is filled automatically at a filling station. The aim of the unit is to increase productivity by 30 per cent or more and to reduce operational costs.
Another unit that raised a lot of eyebrows was John Deere’s autonomous sprayer, a novel unit equipped with a 560-litre spray tank. The sprayer has 1.9 m of ground clearance and four-wheel steering, which makes it extremely versatile. Its aim is to minimize compaction and extend operating windows.
The final innovation in John Deere’s Future Technology Zone was the autonomous drone sprayer. Equipped with a weed scanner and crop sprayer, weeds can be scanned and sprayed from the air. Each unit is equipped with a 10.6-litre tank, which is automatically filled at a field boundary station. When fully charged, each drone can operate for 30 minutes. Recharging takes place at the field boundary station. Precise application is the aim of this drone, significantly reducing overall costs. •