Alternative grain drying systems
MOVING AWAY FROM FOSSIL FUELS AS PRICES SKYROCKET
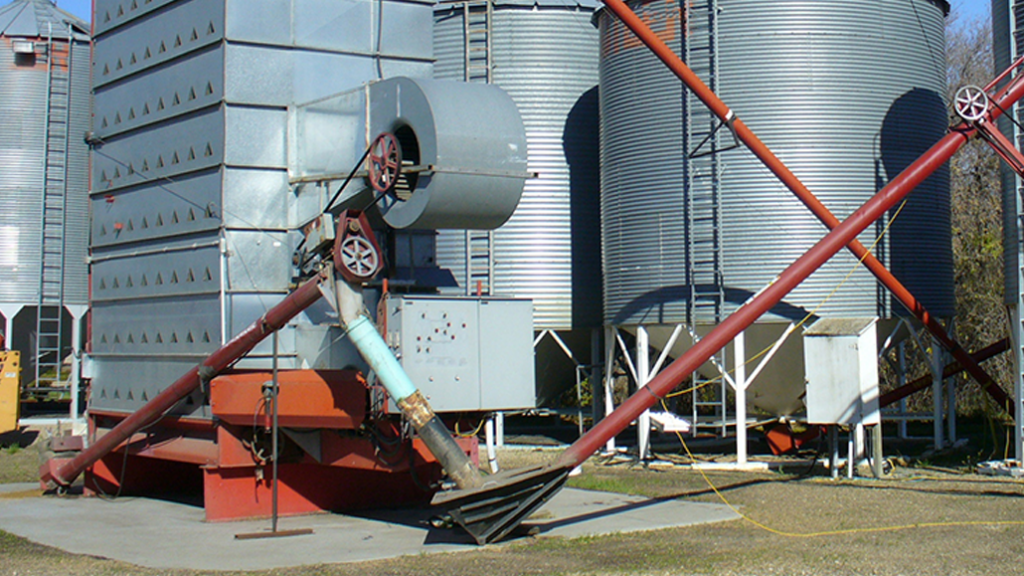
AS PRESSURE FROM the costs and market volatility of petroleum fuels continue to build, Grain Farmers of Ontario and industry partners have been investigating possible alternatives for both commercial and on-farm grain drying, with strides being made in both hybrid propane-biomass and heat pump systems.
WHAT IS A HEAT PUMP?
Dr. David Lubitz, engineer and associate professor in the University of Guelph’s School of Engineering, is involved in a Grain Farmers of Ontario-supported project to improve the energy efficiency of grain drying by using electrically-powered air source heat pumps to pre-heat and reduce the humidity of the intake air.
Lubtiz says electricity has historically not been a cost-effective way of drying grain, let alone heating homes, in part because it has a limited electricity-to-heat ratio — that is, the amount of heat derived from a given unit of electrical energy is one-to-one.
“We don’t generate electricity for home heating because historically it has not been cheaper. From a household heating point of view, heat pumps are getting to the point where they work really well. They’re starting to cost out,” he says, describing the technology as “a refrigerator that you can run in reverse.”
“It’s not making heat, but moving heat from somewhere colder to somewhere hotter. That’s not a natural thing in thermodynamics. We can get several units of heat for the unit of electricity. It’s more efficient when the temperature difference between inside and outside is smaller, which is a challenge.”
OPTIMIZING DESIGNS FOR GRAIN STORAGE
Lubitz and partnering farmer Greg Dineen — who is also an engineer — are constructing a prototype stand-alone dryer on Dineen’s farm to test the viability of heat pump drying. The design will focus on low-heat drying but is capable of being supplied by other forms of heat, such as a propane burner if faster drying is required. This initiative builds off Dineen’s previous on-farm experimentation with heat pump-based bin drying.
“It turns out it’s one of those technologies where you can optimize it for the unique conditions under which it’s working. A higher coefficient performance means more efficiency,” says Lubitz.
However, the need to dry a lot of grain quickly poses challenges for heat pump systems since they are ideally suited to longer, lower heat drying. This means that petroleum-fueled drying will remain a part of grain movement and storage systems.
“If you’re willing to do low temp drying, typically you get better quality, less cracking, and less chance of cooking the grain. Of course, the capacity is lower because the rate goes down. But if you’re willing to only heat a few more degrees, the heat pump gets much more efficient. It can actually be cheaper to run than what you can run in the house,” says Lubitz.
“There is still a place for having surge capacity. That’s how it works now. When the trucks are lined up, you’re concerned about throughput.”
BIOMASS-BASED SYSTEMS
Other technologies have been explored, but like straight electricity, Lubitz says there are many challenges. Solar-powered grain drying, for example, might be a more viable option if Ontario experienced less cloudy weather. Biomass is also being explored, but consistent supplies can be an issue given its myriad of other uses.
“We can make drying more efficient, but it will always be an intensive process. When the weather is good, the harvest is coming in — when you need to dry, you need to dry,” says Lubitz.
If supplies are not a problem, biomass systems could be a solution, just as they have been for other industries, including the greenhouse sector.
Evan Krebs, a Hensall-based grain farmer, custom operator, and mechanical engineering student, is currently investigating the viability of hybrid propane-biomass systems with support from Grain Farmers of Ontario. Early research suggested such systems can significantly improve drying efficiency while lowering costs.
Krebs describes the project as an effort to “look to the future and find alternatives” based on what materials are available to grain handlers in their area. While wood biomass is available in Frontenac, southwestern Ontario provides an abundance of cornstalks. With the right balance between soil health management and stalk harvesting, cornstalks could be very beneficial for grain dryers unable to access natural gas.
“In most cases, propane infrastructure will be available with the existing grain dryer. It offers the ease of propane with the low cost of biomass,” says Krebs.
Krebs says the main difficulty is getting propane equipment approved for use in conjunction with biomass materials. He believes this may result from a lack of insurance precedence for such hybrid systems.
“Currently, we’re trying to design the biomass side of it,” he says. “The bale burning technology is a chunk of it … We need to talk to more experts about the propane regulation stuff.”
TAKING THE LONG VIEW
Finding workable alternatives to propane, natural gas, and diesel fuel will help insulate grain dryers from what Lubitz describes as very volatile price spikes caused by tumultuous events — pipeline and transportation issues and armed conflict being two notable examples.
The elephant in the room, though, is the fact that petroleum is a finite resource, and that, combined with the overarching problem of atmospheric pollution, makes finding alternatives a necessity.
“It’s the long-term point of view. Eventually, the oil is going to run out.” •