Grain monitoring in a digital world
CURRENT AND FUTURE TOOLS
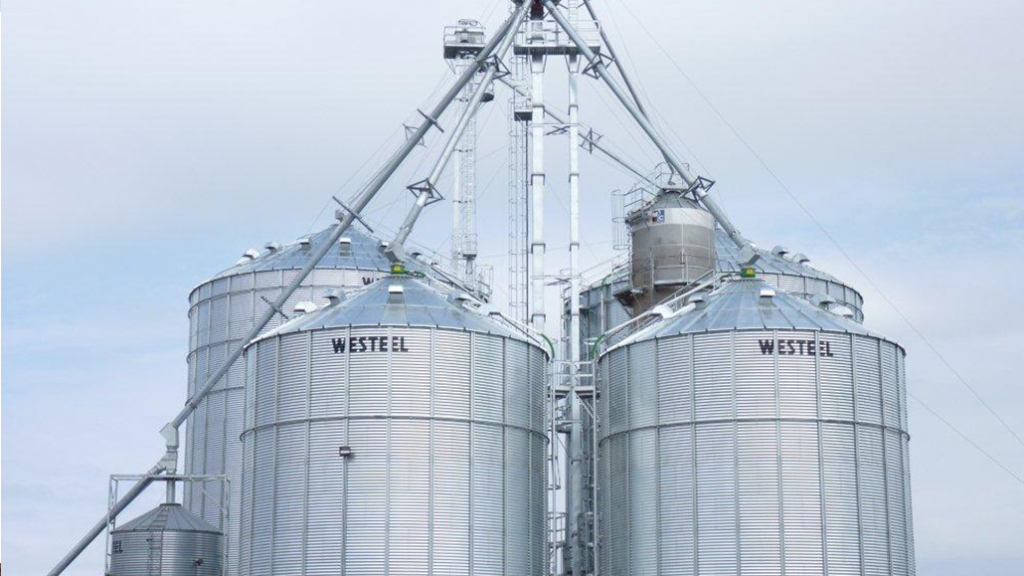
GRAIN MONITORING CAPABILITY is keeping pace with the digital age with more in-depth sensor networks and the capacity for automation; however, that does not mean old school methods have no role. Manually inspecting grain inside the bin, or as it flows into storage, is still critical.
CABLES – THE CURRENT STANDARD
James Dyck, crop systems and environmental engineer specialist with the Ontario Ministry of Agriculture, Food and Rural Affairs (OMAFRA), says in-bin cables are the most widespread and well-established monitoring systems in current use. Designed to hang from bin ceilings, such cables feature multiple points of interaction to measure moisture and temperature at varying levels within the grain mass.
Cables can be used individually or in a network — the latter generally being employed in larger storage structures. With an internet connection, gathered data can be communicated directly to operators. Cables can likewise be linked to fans which could be set to automatically engage if the data indicates aeration is needed.
The limitation of cables, says Dyck, is their inability to measure grain quality beyond a very localized area around the sensors.
“If something is happening six feet away from the cable it’s going to take time for it to get large enough for the cable to detect it…the cable doesn’t replace the need to manually monitor your grain once in a while.”
FROM PROBES TO NETWORKS
Recognizing the need for a more complete picture, Dyck says tools which analyze the bin as a larger network are now available.
Manitoba-based company GrainViz, for example, markets a monitoring product which measures moisture via sensors installed across bin walls. Dyck says the systems gives “an MRI scan of interior water content,” highlighting wet spots and areas where problems might form. At least in theory, the idea is to monitor 100 per cent of the grain mass in order to get ahead of potential problems.
While the cost of such a system might be higher than cables, Dyck believes larger scale sensor networks might be particularly useful for those frequently filling bins in stages.
OTHER TECHNOLOGIES
At the research level, gas analysis tools are also being investigated. Dyck says the idea relies on the “chemical signatures of spoilage” — that is, what chemical compounds are being emitted by the organism or conditions causing reductions in quality. Because even full bins contain a significant amount of air space around and within the grain mass, it is thought sensors looking for spoil-related gases could work much in the same way as moisture or heat sensors.
Currently, there is also focus on rapid testing at pre-storage stages.
If, for example, a chute or auger could be outfitted with what Dyck calls an “in-line” analysis tool, it would be possible to track the quality of grain going into the bin. This could provide a baseline for aeration timing once the grain mass is inside the structure, as well as other business strategies.
“If problems are detected early on or at loading, it might be an opportunity to sell lower quality stuff earlier so it doesn’t go bad on you,” he says.
Automated aeration or alert tools are also available thanks to the general proliferation of digital systems (specifically smartphones, tablets, and other personal computers). The expertise which might be needed to install and connect systems to personal computers is itself widely available.
“Suppliers of that type of equipment can either direct you to an installer or technician which can help you do that.”
Fill level monitoring systems using ultrasonic sensors and Lidar — a method of measuring distance with lasers — are yet another tool type drawing interest.
DON’T GET COMPLACENT
Regardless of the monitoring method, Dyck reiterates grain going into a bin is already at its optimal quality. That quality can only degrade inside the container, meaning growers and elevators should not count their proverbial chickens before the eggs hatch.
“If you don’t know what’s going on you’ll assume no news is good news. The point of monitoring is to go looking and make sure there isn’t something going wrong,” he says. “Just don’t forget about it. Don’t assume when you put it in the bin it will be fine when you take it out. It can be easy to do. You haven’t got paid for it yet.”
MANUAL MONITORING — TRIED AND TRUE STRATEGIES
- Use your eyes: From an aperture on the roof or side, look at the grain mass for wet spots on the surface, potential insect damage, and whether condensation is present.
- Use your nose: Turn on the blower and be mindful of foul odours which might be emanating from quality issues within the grain mass.
- Use them often: Environmental factors both inside and outside the bin affect risk level. Monitoring intervals can stretch up to six weeks in cold months, but in warmer weather, monthly or biweekly checks are preferrable. Don’t assume everything is fine because grain entered the bin in good condition, and under good conditions.
- Use your brain: Always put safety first. Do not enter grain bins unnecessarily. If an individual has to enter the bin for any purpose, ensure all proper safety precautions are taken.