Compaction action
PULLED ELEMENTS
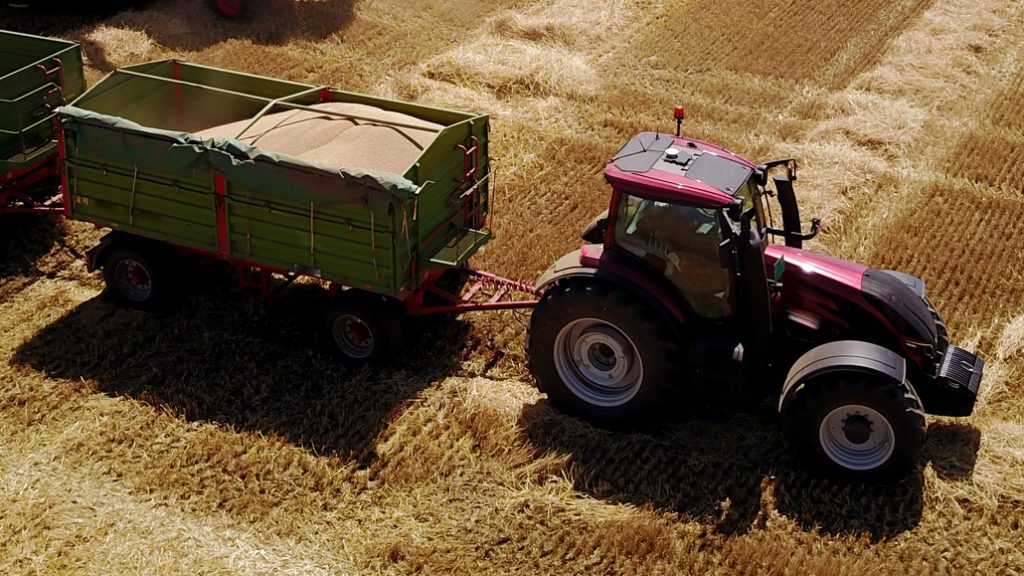
THERE HAS BEEN a lot of talk lately about compaction. We have dealt in recent articles with power units. This time we will consider two very common scenarios with pulled implements. The one may be happening on your farm this month, while the other will happen with the start of wheat harvest. Both activities are common in the harvest process and there really isn’t any way around them. Pictured here is an artist rendition of a two axle bale wagon and a single axle grain buggy. The bale wagon is loaded with 30 large straw bales and has 455/55R22.5 truck tires at 100psi. The grain buggy has 900/60-32 Radial at 27psi. This equipment was tested at IFAO’s Compaction Action event.
Before comparing the two pulled implements, let’s briefly describe what the soil under the equipment has to endure. A soil profile will typically consist of at least two soil horizons, the top horizon (A) is a layer of top soil that is about six to 12 inches thick, and the second horizon (B) is a layer of subsoil below that. Soil scientists will likely hate this oversimplification but it is the easiest way to talk about how the different soils are impacted by compaction. The strength of these two horizons is compared using compressive strength, which is measured as the pressure (or stress) required to cause a permanent change in shape. The stress required to cause a permanent change in shape are on average 14.5 psi for topsoil and 7.25 psi for subsoil. Asphalt has a compressive strength closer to 3,000 psi.
Wherever you drive, the ground underneath has to support the vehicles weight. If you drive over anything enough times, it starts to get harder and harder until it will eventually hold the weight. Roads that are designed to carry weight are easy to build. You compact non-shrinking fill like stone or sand to the point where the heaviest vehicle it needs to support can’t compact it any further. Soil that needs to support crop growth can’t be compacted to the point where it can support huge loads, so we have to be very careful about how the load is applied.
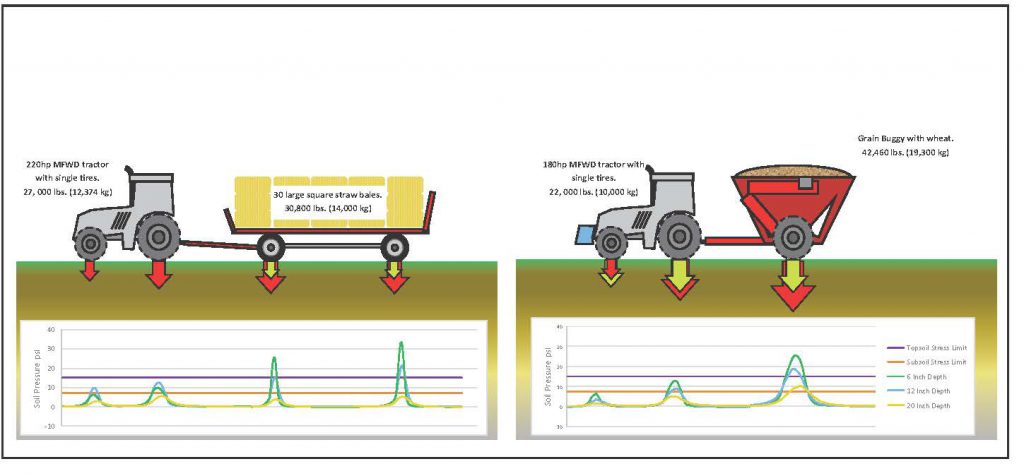
TIRES
Increasing the number of tires, changing the tire technology and lowering the air pressure helps to distribute the load over more area and reduces the stress and the damage to the surface. However there can still be damage done deeper in the ground simply due to the sheer mass of the implement. Since the topsoil can handle more stress than the subsoil before it deforms, driving over soil is similar to driving over an old bridge. The decking on the bridge might be strong enough to not break under your tire, but the trestles underneath may not support the decking and the load at all. The old gleaner combine with the small tires at high air pressure might break a board on the bridge deck but the bridge structure can carry the entire load. The class 9 combine with low pressure float tires won’t break a board, but the entire bridge might collapse. In the field at the Compaction Action event, low pressure tires spread out the load enough that damage to the topsoil was avoided; however, the total weight of the equipment is still heavy enough that the subsoil cannot support the load and damage can occur deeper. This deep compaction becomes very difficult if not impossible to correct.
Looking at the two situations illustrated, the red arrows indicate the relative axle weights of the loaded equipment. The yellow arrows show the axles that will change weight when the implement is unloaded. On the two axle bale wagon, none of the load is transferred by the tongue onto the tractor, so the tractor axle weights will stay the same with bales on the wagon or not. The grain cart does transfer some load to the tractor tires which will increase the weight of the back axle while decreasing the front. The tractor on the grain cart was pretty well balanced when the cart was unloaded, but there could be some improvement made to the balance of the machine by moving some ballast from the rear axle to the front. Adding weight to the front of this tractor may help with traction on the front tires when the cart is loaded. For the bale wagon, the ballast is not required since there is no tongue load to offset, and removing the ballast from the front of the tractor would help reduce the total weight which helps reduce subsoil stress.
SOIL PRESSURE
The two plots at the bottom of the graphic show the soil pressure at depths of six, 12, and 20 inches. The green line for the six inch depth is below the 14.5 psi (purple line) for the tractor in both situations which means that the tractor is not loading the topsoil enough to cause damage. The blue line is the subsoil stress at 12 inches. All of the axles except for the front axle of the tractor (left peak on the plots) exceed the threshold of subsoil stress. The axle load in both of these scenarios are heavy enough to cause some amount of deep compaction. Looking at the far right peak on each plot, the rear axle of the wagon has about eight tonnes, and the axle on the grain buggy has about 18 tonnes. The large tires on the grain cart help reduce topsoil stress and may not leave a rut like the truck tire on the hay wagon but the 12 inch pressure is roughly the same. The large axle weight of the cart does significantly increase the pressure at the 20 inch depth compared to the wagon.
In conclusion, it’s important to think about the entire setup when trying to offset the potential for soil compaction. To be able to really make proper management decisions on how to reduce the potential for soil compaction, it’s important to know equipment weights when loaded and how the loads distribute across and between the implements. The compactive forces may surprise you in how they distribute across the implement configuration. The buggy in this scenario carries more potential for compaction despite the use of bigger tires because a significant amount of the load is transferred to the tractor. The higher weight of the buggy, despite using big floatation tires, results in less topsoil compaction but more deep compaction even though the bale wagon uses high inflation truck tires, something most would consider a poor choice. So while inflation pressure changes can be used to reduce compaction, the full mass of the implement may still transfer significant stress deep into the soil.
This article is part of a series highlighting lessons learned from the IFAO Compaction Action Day. Demonstration results, detailed demonstration set-up information, and a series of videos featuring the experts and topics from this day can be found at www.ifao.com. •