Seed development: corn
BREEDING NEW LINES, TESTING NEW HYBRID CROSSES
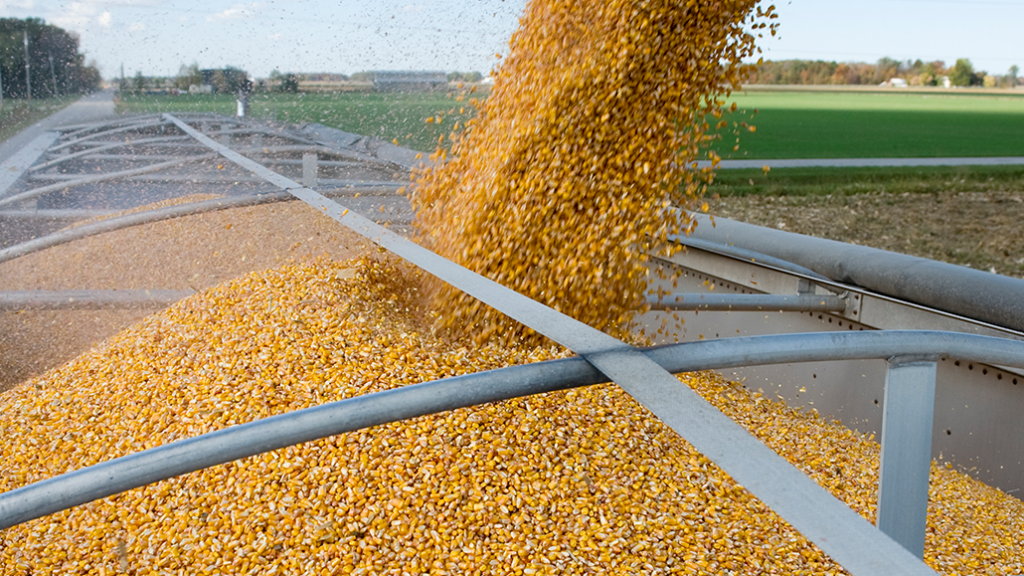
FARMERS KNOW WHAT is going on in their fields during the growing season, but are we all aware of what goes on prior to the seed arriving in our sheds?
This article is the first in a series that will explore the process of seed development.
Shawn Winter, product development manager with Maizex Seeds Inc, explains corn breeding and what it takes to get a corn hybrid commercialized. Dave Harwood, technical services manager with Corteva Agrisciences, describes the process after a successful hybrid has been created, until that corn seed ends up in your shed.
There are commonly two sides to a corn breeding program, breeding new lines, and testing new hybrid crosses. The breeding side of the program is where the corn breeder creates populations using known inbreds that work well in each maturity zone. With these populations they select for phenotypic and agronomic traits that would be beneficial in the hybrid.
New inbreds are placed in small trials with one or two repetitions in several locations where they will screen out the worst inbreds. The preferred inbreds will then be crossed with known inbred lines to create hybrid combinations and are then tested to see if they produce successful crosses. Once the breeder has taken a couple of years to assess how successful the combinations are, the inbred crosses then enter the hybrid testing network.
In the hybrid testing side of the program, corn companies can access material from genetic suppliers from around the world and/or from their own breeding programs.
Breeders take products of interest and then test them in small plots across a few locations while they get comfortable with the genetics.
“Hybrids are recommended for a targeted environment based on previous experience with related lines, it’s very rarely a truly unknown situation,” notes Winter.
Once a breeder is comfortable with how the hybrid behaves, they will increase the number of trial locations to further test the yield and agronomic stability of the hybrid. This level of assessment will occur for two to four years at multiple sites. If everything still looks promising, it will then be placed in pre-commercial strip trials; and if it passes through all of the company’s objectives, would then be commercialized.
In this system, the breeder and production team will have experience with the hybrid for three to four years before a farmer would be able to purchase it for their farm.
When screening for disease tolerance, Winter explains they work closely with Albert Tenuta, field crop pathologist with the Ontario Ministry of Agriculture, Food and Rural Affairs, and participate in disease screening trials.
For some trials they rely on natural infection which can be difficult in some years when weather patterns do not cooperate. A significant effort also goes into looking at DON in corn, a troublesome disease for Ontario corn. Winter and his team are aiming to mimic what farmers see in fields, as opposed to an inoculation nursery system which is the standard method of testing currently.
Ontario has such a diverse, variable climate, “it’s all a balance,” says Winter, “of having the right number of locations in the right maturity areas.”
Through experience, breeders learn the locations that have high or low yields, which areas behave similarly, or vise versa. They also look for areas of uniqueness, with the hope they will find varieties that do well in drought, or be able to target areas that have specific insect or disease pressure.
Another area they look at is different field management strategies such as high and low populations, how fungicide applications impact the hybrid, high nitrogen rates, and crop rotations.
“Whether it is corn, soybeans, or any other crop, breeders are all trying to do the same thing, get the most data for the hybrid/variety that they are working on to be able to recommend positioning in the right place for the farmer’s success in their field,” says Winter.
Once a hybrid has received the gold stamp of approval from a breeder or company, it will then be placed into commercial hybrid corn production.
COMMERCIALIZATION
Commercial production of hybrid corn begins with a small amount of inbred seed being delivered from the breeding program, where the seed will be increased for larger commercial production. Most companies will do their base seed production in unique locations, often the Pacific Northwest, where there is low corn production to avoid any corn pollen from other fields contaminating the inbred increase.
Seed from these increases are then delivered to the production facility.
“Many production and handling facilities are in the Chatham-Kent area for corn hybrids in Canada,” says Harwood.
Hybrid seed production fields are then planted in strips with inbred A and inbred B planted in four rows of seed parents and one row of the pollinator parent across the field.
Farmers will plant the seed on rotated ground that is isolated and the seed companies then take over and manage the fields, inspecting for various agronomic issues.
“Inbreds that are used to grow corn seed need a lot of babysitting, so the fields are monitored very regularly,” says Harwood.
As the crop begins to flower, detasseling is required of the seed parents, so that the male inbred rows can pollinate the female rows and that is where hybridization happens.
After pollination, the male plant is chopped out, so that the nutrients from the field only go into further development of the female plants. Once the ear has developed and the moisture of the corn kernels are around 35 per cent to 25 per cent, the crop is harvested. It is harvested on the ear, to ensure that the seed is handled gently. Ears are inspected as the material comes into the facility, by electronic and visual inspection, any off types are removed.
The seed is then slowly dried on the ear using a low temperature. If it is dried too quickly at hotter temperatures, the seed can stress crack, affecting the seed quality and germination.
After drying, the ears are put through a sheller, where the seed is then placed in bulk storage.
Over the winter, the seed is conditioned (sized, treated, and bagged). Seed is tested for its ability to handle difficult conditions, such as under cold conditions at planting to see how the seed behaves. If there are genetic and physical differences between batches of seed, the batches that are unacceptable are removed. Then, only after all the boxes have been checked, will a bag of hybrid seed corn be delivered to seed dealers across the country, then into a farmer’s shed for planting during the upcoming spring.
When asked about seed treatments, Harwood commented that things have changed drastically in the past 35 years. Many years ago, the industry used Captan as a fungicidal treatment, now there is a combination of four to five fungicides applied on the seed, and in general an insecticide of some type.
Lumivia has greatly replaced neonicotinoids which were used for 15 years, prior to them being phased out. Increasingly, biological seed treatments are now being applied, which can promote seed protection or growth.
“Seed treatments have gone from very simple with some protection to an incredible level, which is comprehensive and complex. It is constantly reviewed- are we using the best package available?” says Harwood. •