Automation and farm jobs
STUDY ESTIMATES ONE-THIRD SMALLER WORKFORCE
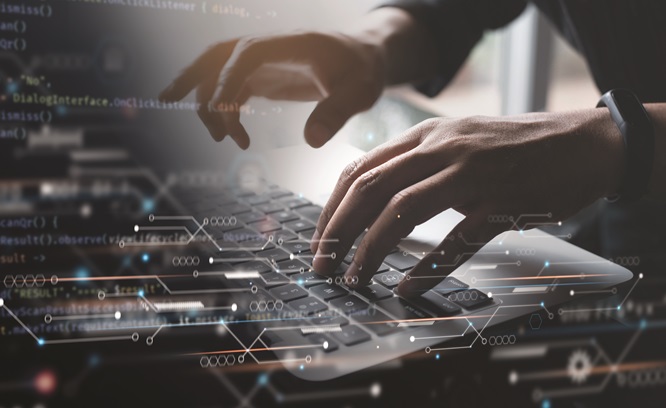
WILL AUTOMATION TECHNOLOGY REPLACE ONE-THIRD OF ALL AGRICULTURAL PRODUCTION JOBS? A recent report from The Conference Board of Canada, a national research and analysis firm, says it’s very possible. Indeed, the same report also says an additional one-fifth of jobs in food and beverage manufacturing could be similarly replaced – and all within the next 10 years.
Some in Ontario’s agriculture sector, however, are less convinced. While automation is increasingly common on farms and elsewhere in the food supply chain, what “could” happen may not match what will happen, at least in the short term.
AUTOMATION ALREADY HAPPENING
The Conference Board report highlights routine and repetitive tasks within agriculture and the food sector are at greatest risk of replacement by automation. Russell Hurst, executive director of the Ontario Agri Business Association (OABA), doesn’t consider this assertion particularly novel, given many farms and other businesses have been steadily moving towards automating such processes for some time. One member of OABA, for example, recently installed an automatic bagging system as part of its pre- mix livestock feed line.
“It can be expensive. But when you ask the plant manager, the robot doesn’t get sick, doesn’t take days off…Those can be big issues for a company,” says Hurst.
The diversity of the farm and food sector, however, makes it hard to predict when widespread change will be realized industry-wide.
“We’ve been using machine learning and AI for years now. It’s not like someone flipped a switch,” he says. “Everybody adopts technology at a different pace. The automotive sector is one end of the spectrum because it’s a small number of companies that can implement change. But OABA alone has 500 members. A lot of it, in some cases, is probably due to wiliness to change.”
Hurst adds willingness to change may also be affected by other considerations, such as reducing the number of food safety “touch points” a product passes through as its being processed. Fundamentally, establishing the return on investment for any piece of technology is critical and unique for each business.
“Will replacing someone account for days off, competency, or training time? It’s not always those traditional straight-line return- on-investments.”
NEW OPPORTUNITIES
With specific regard to primary agricultural production, Hurst says technology adoption tends to be “more of a slow burn,” with few – if any – truly game-changing technologies being widely adopted overnight. Results from Purdue University’s annual Precision Survey, for example, continue to reinforce this trend.
It is possible to see a reduction in personnel over time, though – at least in some places.
Citing another feed mill member of the association, Hurst describes a recent visit to one of its facilities as “eerie” due to the lack of people in parts of the plant, which may have once had 15 to 20 employees on the floor at any given time. It’s not to say those jobs were all lost, however. Instead, many positions have shifted from a physical floor job to a managerial position. That is, managing the process rather than the product directly.
Hurst’s example highlights another conclusion from the Conference Board of Canada report – that jobs in information processing, product design, software engineering, and other related fields will be increasingly common. An excerpt from the report reads:
“Although information technology occupations account for a very small share of sectoral employment, those projected to grow the fastest over the next decade include data scientists and software engineers. The skills most in demand for the future agriculture workforce are product design, digital production, and digital literacy, while the food and beverage manufacturing industry will be looking for skills such as digital literacy, problem-solving, evaluation, systems analysis, and monitoring.”
For Peter Sykanda, farm policy advisor with the Ontario Federation of Agriculture, the evolution in job type will likely run into the perennial problem of attracting and retaining employees. Even if automation means the number of labourers required is lower – a scenario that is not guaranteed – getting qualified people to live and work in rural areas is likely to be an issue for some businesses.
Another perennial problem, the availability of high-speed broadband internet in rural areas, will confound the adoption of new technologies. While Sykanda says Agriculture Agri-Food Canada is “frantic” in encouraging tech adoption, particularly as the government sees it as a way of improving efficiency and reducing greenhouse gas emissions, there does not appear to be a significant body of policy directly supporting tech adoption.
“They see, as we do, high-speed internet and tech adoption does come with an efficiency often in a fuel or energy use, or fertilizer use area… We need to help governments recognize linkages between tech adoption and desires for emission reduction and help our farmers continue to be competitive in a global marketplace,” says Sykanda, adding he considers the Conference Board’s overarching conclusions to be ambitious.
He also reiterates there will always be a need for “that discerning mind and gentle touch of a human” in agricultural production. •