Understanding precision agriculture
ARE YOU AND YOUR EQUIPMENT IN SYNC?
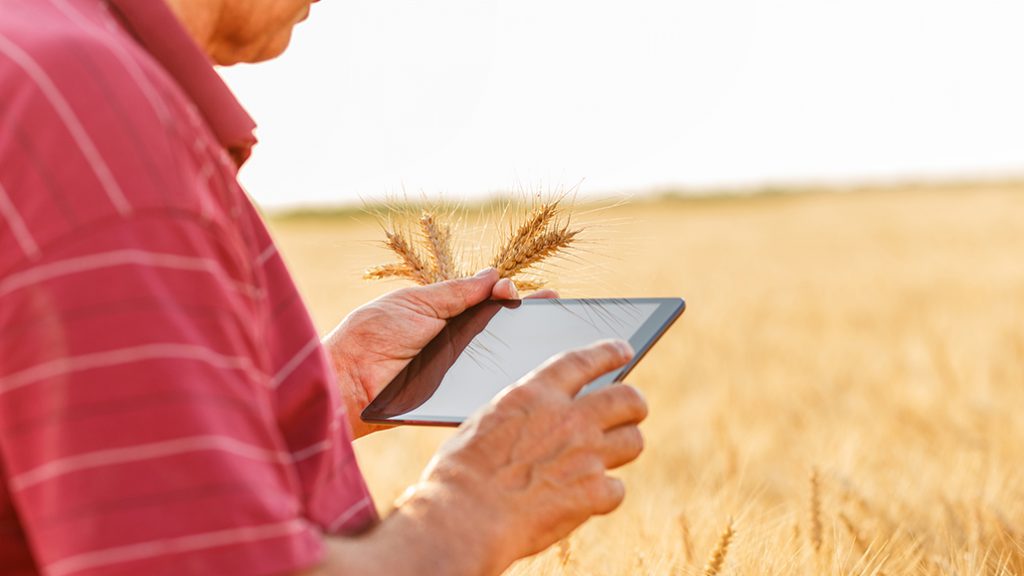
YOU CAN’T MANAGE what you don’t measure.
The more accurate, useful yield data a grower can collect from their precision equipment each season, the better equipped they will be to make more informed management decisions for each of their fields.
Poor, inaccurate, or incomplete yield data can have long-term consequences for many seasons to come. That’s why growers need to make sure their precision system is fully calibrated and operating exactly as it should — well before the start of harvest.
Greg Kitching, integrated solutions consultant with Premier Equipment, and Shawn Redick, precision ag manager at Delta Power Equipment, are industry cooperators of the Precision Agriculture Advancement for Ontario (PAAO) project. They say the most common pre-harvest issues can be avoided and offer a few tips for maintaining and calibrating precision equipment.
GOOD WORKING ORDER
The first simple step in getting equipment ready for harvest is to make sure it’s clean and in good working order. Redick says growers should focus their attention on the components that tend to face the most wear and tear.
One common trouble spot is the grain elevator, where all the yield measurements take place via an impact sensor at the top of the elevator, or an optical sensor high up the elevator. These sensors measure the volume of the crop flowing through the combine.
Both the impact and optical sensors, says Kitching, depend on the grain elevator chain to function properly.
“If that chain is worn or damaged, or the paddles on it are misshapen, that can skew your yield results,” he explains.
Kitching adds that if harvest conditions are especially wet and muddy, growers should check the impact or optical sensors after every 50 hours of use to make sure they are clean and free of debris.
Once general maintenance is squared away, growers should then install any necessary software updates — typically for their displays and GPS receivers, but there may also be additional drivers and updates for other components.
It might seem like a minor point, but not keeping all the software up to date (or updating the software on the display and not the GPS receiver) can lead to several potential issues with reading yield data, says Kitching.
“One issue that I’ve seen is that multiple pieces of precision equipment can get out of sync and have trouble communicating with each other,” he says. “Sometimes the actual frequencies that the satellites work off will have changed, and you may only get part of the yield dataset.”
“You could even risk getting inaccurate results, or having a yield monitor that won’t read the data at all,” adds Redick.
Another common problem that can lead to frustrating issues is not switching the grain type on the yield monitor to the crop that is currently being harvested.
Combining with the wrong grain type selected — wheat instead of corn, for example — would tell your system to use the wrong yield calibration settings which can also throw off yield measurements.
CALIBRATION
When it comes to calibration, growers should use a weigh wagon to do three to five consistent-sized test loads (3,000 to 5,000 pounds of crop) in each crop that’s being harvested. This, says Redick, gives your yield monitor a good average from your fields. Growers should also calibrate their yield monitors at different flow rates or bushels per hour.
A good way to adjust for different flow rates is to do test loads at slow, medium, and high speeds. This helps build the accuracy of the algorithm your yield monitor uses to calculate yield.
“Every single one of your fields is going to have variability in it and that’s what you’re trying to measure since you can have one field running 100 bushels and another field running 60 bushels,” explains Redick. “The sensors that measure grain weight or flow act differently when there’s a low flow rate versus a high flow rate, so you want to be able to calibrate for that yield curve.”
SAFE AND ORGANIZED
Once growers collect yield data, there are recommended ways to keep it saved and organized for when they or their crop advisor need to access it.
The most common, tried and true method, say Kitching and Redick, is for growers to copy yield data off their display to an SD or USB key, and then move the files to a series of folders organized by date and field on a desktop computer.
If a hard drive fails, or in the event of fire or theft, growers need to have some sort of backup strategy in place so that years of valuable data don’t vanish. One solution is to have a secondary, off-site computer or hard drive where files can be stored. Another, is to take advantage of free, cloud-based storage services, such as Google Drive.
Kitching notes that, in the last several years, many precision ag systems have introduced their own cloud-based storage systems, such as MyJohnDeere and Case IH AFS Connect, where yield data is automatically uploaded to a secure server from the display.
“Whether you’re calibrating equipment, or organizing and saving your data, know that from the outset you need to put in the time to make sure you’re getting everything right,” says Kitching. “Good yield data is like the report card for your fields, and you want to make it as straightforward as possible to analyze the decisions you made and measure your success.”
Growers should refer to their manuals and display controls for operating procedures specific to their equipment models.
This project was funded in part through Growing Forward 2 (GF2), a federal-provincial-territorial initiative. The Agricultural Adaptation Council assists in the delivery of GF2 in Ontario.
Precision Agriculture Advancement for Ontario: This article is part of a series dedicated to helping farmers understand and implement precision agriculture technology. It is based on research conducted by Nicole Rabe, Ian McDonald, and Ben Rosser at OMAFRA, in conjunction with Mike Duncan, Sarah Lepp, and Gregor MacLean at Niagara College.
For more on precision agriculture go to: www.gfo.ca/Research/Understanding-Precision-Ag. •