Supply chain resiliency
MAINTAINING THE FLOW OF GRAIN DURING COVID-19
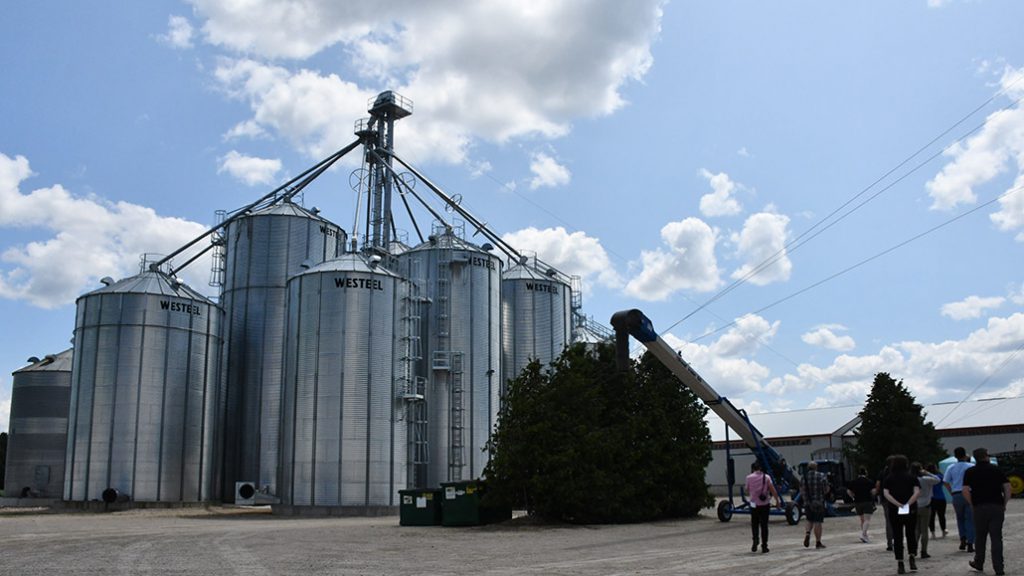
WHAT YOU NEED TO KNOW • COVID-19 was declared a global pandemic on March 11. • COVID-19 is an infection caused by a coronavirus. Symptoms range from mild to severe, including cough, fever, difficulty breathing, and pneumonia in both lungs. In severe cases, infection can lead to death. • The Government of Ontario issued an Emergency Order on March 17. One week later, Premier Doug Ford ordered the closure of all non-essential businesses in Ontario. Agriculture is deemed an essential service and permitted to continue operations. • Agriculture supply chain concerns resulted from consumer panic buying and a shift in demand for specific products, forcing grocery stores to limit purchase quantities. • Some meat processors and food manufacturers have been forced to close due to employees diagnosed with COVID-19. |
HOW ROBUST IS the grain supply chain in managing crisis situations such as the COVID-19 pandemic? According to farmers, merchants, processors, and retailers, contingency plans are not always comfortable — but they are very doable.
ON THE FARM
For Matt Beischlag, a grain farmer near Hagersville, contingency planning means extrapolating biosecurity practices from his broiler chicken barns to the grain business. That includes minimizing interactions with suppliers by calling ahead for parts, having all inputs delivered in advance, and ensuring sanitation supplies are available for everyone operating equipment.
“With the chickens we are pretty tight with our biosecurity already so it’s pretty easy to do. It’s just branching off what we’re already accustomed to,” Beischlag says.
He only employs a few seasonal workers during busy parts of the year, but this year, Beischlag made sure someone other than himself knew how to operate specific pieces of equipment (such as the planter). This ensures a backup operator in case he gets sick.
His business already has grain forward contracted for several years, which Beischlag hopes will guarantee a substantial portion of his sales for the foreseeable future if there are market interruptions.
FOR THE SEED DEALER
“This social distancing is a little hard on everybody. For farmers, no one-on-one, that’s hard to do,” says Leo Guilbeault, an Essex County farmer and Pioneer Seed dealer.
Though farmers might chafe at the necessity of social distancing and extra sanitation procedures, Guilbeault says such measures do not have a major effect on how they receive or ship inputs.
As a seed dealer, he says, about 65 to 70 per cent of his customers have seed delivered directly to their farms. The lack of handshakes aside, those deliveries continued in a more-or-less normal way this spring.
“The plan was to set up a day with farmers. They park their wagons, and we fill them,” says Guilbeault. He adds the same process applied for those picking up seed — and they did ask visiting farmers to stay in the tractor to minimize contact.
Delivery slips migrated to an email format whenever possible. Extra precautions were taken in cases where electronic exchanges were not possible.
“Especially in the seed business, we want deliveries signed all the time because of intellectual property rights. That was the trickier part,” he says. “But planting is going to happen whether there’s a virus or not.”
AT THE ELEVATOR
For Quentin Martin, owner and co-chief executive officer for Cribit Seeds — a grain elevator and Dekalb seed dealer in West Montrose — technology has been a major factor in allowing operations to continue in a (mostly) normal fashion.
In terms of seed delivery, the use of a ‘hitchhiker’ forklift allowed for no person-to-person interaction.
“Technology has allowed for delivery of product on farm without the need for it. We all crave the interaction, but we can get though the season without it because of one simple technology like that,” he says.
Martin reiterates their staff have been critical in all aspects of business operations. To ensure those staff are as protected as possible, all major health recommendations in terms of distancing and sanitation are being followed. This includes interacting with shippers using virtual technology whenever possible, ensuring employees that can work from home are doing so, and actively cleaning all common areas and services.
“Part of it is understanding the stress of staff too,” says Martin, including assuring them things are going to keep operating despite temporary shut-downs.
For their processing facility, Martin says upgrades made in 2019 have allowed them to increase efficiency by clustering production.
“We can shut things down for larger chunks of time. It gets people some time away,” he says. “It’s amazing how taking about seven people out of the physical facility makes managing the space so much easier.”
When asked about reducing the impact of potential labour shortages, Martin reiterates automation playing a critical role.
“We have two bagging lines. Within the past two years one has been fully automated from bag-pickup to palletizing, and the other has a palletizer,” he says.
Martin believes much of the fear regarding supply chain vigour stemmed from end consumers moving inventory from store shelves to their homes through mass buying. Such behaviour means manufacturers have been forced to move more product more quickly.
“This will lead to a pause at some point. It’s just bizarre for something like pet food, the chasing of ingredients to get some bulge down the supply chain and make sure shelves are not empty,” says Martin.
IN THE FLOUR MILL
Automation and comparatively low labour needs in grain processing are a major safety valve for millers during the COVID-19 pandemic, says Buck VanNiejenhuis, general manager for Ardent Mills Canada.
At Ardent’s Mississauga location, for example, VanNiejenhuis says the mill employs about 30 to 35 employees, which are separated on several different shifts. Like other businesses, further efforts have also been made to reduce risks for employees given the current pandemic.
“There’s never a lot of time where you see a lot of people in the same space, so there’s limited risk there. We don’t forsee a labour shortage,” he says.
A significant outbreak at any facility, however, would still pose a challenge. In such a case, VanNiejenhuis says the large networks of facilities characteristic of large millers, such as Ardent, inherently provide contingency options.
“Typically, if there’s a supply issue somewhere they can pull from other regions. In this instance trucking companies have been very open and forthcoming. Rail lines are doing what they can. Everyone is partnering very well.”
ON STORE SHELVES
Ensuring employees and customers stay healthy is the most important aspect of supply chain and labour resilience in the retail sector, according to Jason McLinton, vice president of grocery division and regulatory affairs for the Retail Council of Canada (RCC) — the national advocacy group for Canadian retailers.
In practice, that means enacting an enormous variety of procedures.
While individual retailers make decisions specific to their own stores, McLinton says regular and intensive cleaning regimens, shifting to touchless payment systems wherever possible, and placing limits on purchase quantities for key items (to prevent hoarding) are all examples of employed tactics.
“Our primary purpose is to protect health and safety first, then get goods to people when they need them,” says McLinton. “The number one thing we are concerned about is people are safe and feel safe at work.”
“We have been going flat out to make sure Canadians have access to the goods they need when they need them.”
RCC held meetings in April with all levels of government, federal agencies such as the Canadian Food Inspection Agency and Agriculture and Agri-Food Canada, as well as national and provincial farm groups to address critical concerns — including ongoing labour-shortage issues related to temporary foreign workers.
“We’re certainly facing labour challenges now and likely will moving forward. That’s true in retail, for producers, and processors,” he says.
However, the myriad of partnerships formed between retailers and their individual suppliers also allows for flexibility in contingency planning.
“Every retailer will be different, but they are very nimble and have great relationships with their suppliers,” says McLinton. •