Save money on grain drying
INSULATION, ALTERNATIVE FUELS, BETTER DESIGNS
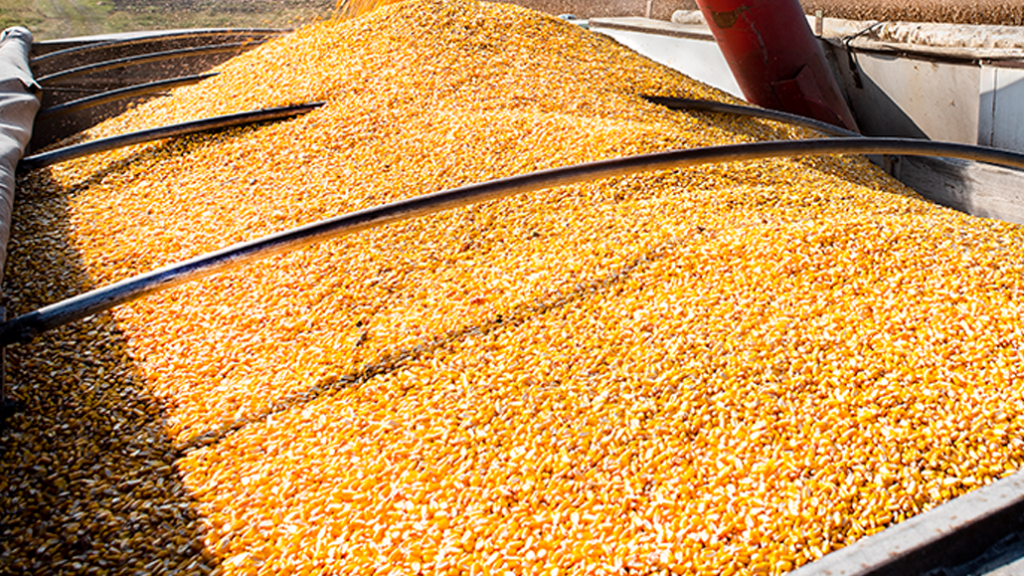
GRAIN DRYING IS not a cheap process, even in the best of times. With record-setting fuel prices, reducing drying bills has become even more essential.
Grain drying technology is well established, and the expense of installing new systems is burdensome. While options may be constrained, close analysis of individual systems and operation characteristics can help grain handlers find opportunities with what’s already on-site.
SOME TIPS
Do the calculation: A critical first step is understanding how much energy is being used, says James Dyck, crop systems engineering specialist with Ontario Ministry of Agriculture, Food and Rural Affairs (OMAFRA). That doesn’t mean just looking at fuel bills and bushels dried. Analyzing the number of cubic litres used against grain volumes and other factors like average moisture highlights the true number. Prices change, after all, while energy volumes may not.
Dry just enough: Control systems with more accurate readings go a long way, allowing for the more effective monitoring of moisture sensors to ensure grain is not being heated more than necessary.
“You don’t want to find out you dried 1000 bushels of corn to 10 per cent when they only needed to be 15. That’s wasted fuel,” says Dyck.
What can your system do? Grain dryer systems are meant to last decades. Assuming the dryer is not up for replacement, operators can contact their dealer or the equipment manufacturer for additional information about their on-site system and any optimization opportunities. Dyck says those in the market for a new dryer might want to consider designs with heat recovery capability — that is, systems capturing air at lower sections within the bin, where grain is drier, and up-cycling it.
“Lots of new dryers have that, but lots of manufacturers have retrofit kits available too, especially for the larger dryers,” he says.
Maintenance and insulation: Keeping burners clean and free of fines (very small particles) is important for burner efficiency. Finding ways to reduce air cooling between the burner and the grain column is another potential option, particularly for exposed ductwork.
Dyck reiterates that even a small amount of heat loss while air is in-transit can amount to significant costs and that insulation material needs to be suitable for the outside environment, as well as machinery vibration.
“A small percentage of a million BTUs is significant. You can’t just slap anything on the duct, but it is an opportunity to save a bit.”
Moving grain: Dyck says cooling grain in the bin after running the dryer in full heat mode is an option for gaining “a bit” of energy efficiency.
“You can pull corn at 17 to 18 per cent instead of 15 per cent, for example. Pulling the grain to another [location] removes the last percentage,” says Dyck. However, he adds handlers usually need a bin which is slightly larger than average. Time is also required since the cooling process can take 10 or 12 hours.
“You need to have all your infrastructure sized appropriately.”
ALTERNATIVE HEAT SOURCES
Petroleum isn’t the only thing that can burn, of course. Biomass-fueled burners are common and employed to great effect in many industries, such as greenhouses. Dyck says finding an energy-dense fuel source for grain drying is possible. Indeed, some suppliers have grain drying options, though Dyck says he has not seen any in person.
“The challenge comes with scale. With grain drying, you need a lot of heat very quickly. The biomass system may get quite large… With any of this, it’s a high-intensity thing you do for a couple months,” he says.
“Grain dryers are simple machinery. Heat, auger, and a fan, and there are not a lot of places in that design to find savings. Make sure the dryer is sized for what you need. Other than recapturing the wasted heat, that’s probably the best option.”
RESEARCH INTO NEW TECHNOLOGY
Attempts to lessen energy bills and find reliable sources of heat have prompted Evan Krebs, a Hensall-based grain farmer, custom operator, and mechanical engineering student, to investigate the viability of hybrid propane-biomass systems.
With support from Grain Farmers of Ontario, Krebs aims to improve grain drying efficiency while reducing greenhouse gas emissions. As described in a project proposal submitted to Grain Farmers of Ontario, initial research suggests hybrid propane-biomass fuel systems have considerable potential.
“In most cases, propane infrastructure will be available with the existing grain dryer. It offers the ease of propane with the low cost of biomass.”
Krebs describes the project as an effort to “look to the future and find alternatives” based on what materials are available to grain handlers in their area. While wood biomass is available in Frontenac, for example, Southwestern Ontario provides an abundance of cornstalks. With the right balance between soil health management and stalk harvesting, cornstalks could be very beneficial for grain dryers unable to access natural gas.
Getting propane equipment approved to be used in conjunction with biomass materials is one of the main challenges, Krebs says. He believes this may result from a lack of insurance precedence for such hybrid systems.
“Currently, we’re trying to design the biomass side of it,” he says. “The bale burning technology is a chunk of it…We need to talk to more experts about the propane regulation stuff.”
CONTRADICTORY WANTS
Krebs reiterates that any system must be operationally efficient and economically suitable — providing lots of heat and air for short periods of the year. The agronomic cost of residue removal will also be critical, particularly considering the high costs of fuel and fertilizer.
Even if petroleum prices were in the realm of reasonable, Dyck considers higher-than-desired drying costs will continue to be a reality as growers continue pushing yields and heat units. It’s a reality that has him wondering if a tipping point might eventually be reached.
“Historically, even with drying, it does seem to be more profitable with higher-yielding varieties. Eventually, drying, in theory, will be so expensive it starts to make sense to grow something you can manage more efficiently,” he says.
“Long season growth and low drying costs — you get one, not both.” •